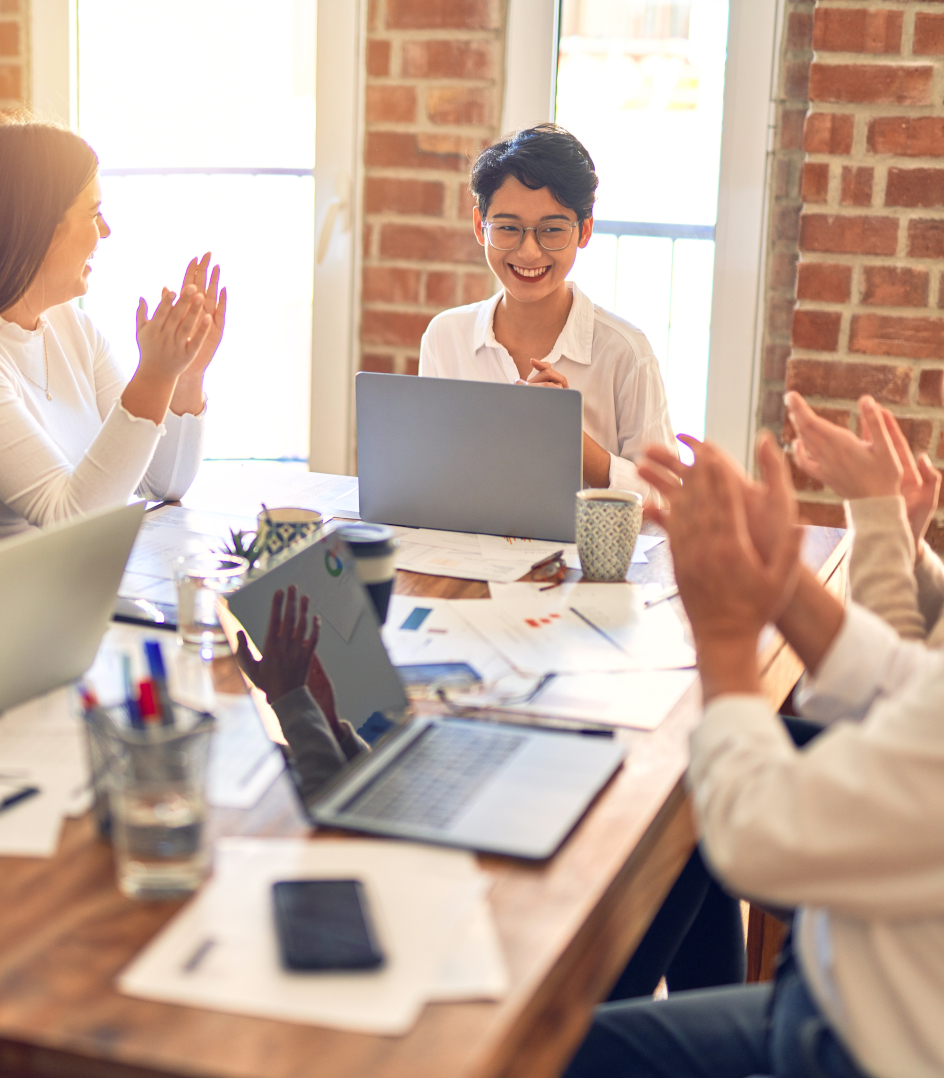
Abriendo camino a Lean Manufacturing
Independientemente de la industria, existen tendencias claves del mercado que afectan a todas las empresas hoy en día. Considerado por algunos como la Cuarta Revolución Industrial, cambios extraordinarios en la forma en que las personas se conectan, detectan, responden e interactúan con datos, aprendizaje automático, inteligencia artificial, sistemas inteligentes e IoT (Internet of Things), están cambiando todo sobre la forma en que una compañía necesita llevar a cabo negocios.
Como resultado, los clientes demandan una comunicación cercana y activa, así como un tiempo de respuesta cada vez menor que ayude a facilitar sus necesidades. Para que el negocio moderno sobreviva y prospere, hoy en día necesitan adoptar el cambio como parte de su ritmo habitual o se correría el riesgo de que los competidores nos superen. Para avanzar eficazmente, muchas empresas están adoptando principios Lean Manufacturing para resolver sus desafíos de entrega e innovación. La adopción de esta práctica incluye hacer varios cambios en la forma en que una empresa opera y ofrece valor.
Lean y sus principales herramientas
JIT (Just In Time)
Sistema “Pull” o de arranque basada en producir sólo lo necesario, entendiendo como tal no lo que viene establecido en un plan, sino lo que los clientes demandan.
Objetivo 5S
Lograr la eliminación de despilfarro en diferentes áreas para desarrollar cualquier sistema de producción enfocado a la satisfacción del cliente, mejoramiento del medio ambiente y desarrollo integral del personal operacional.
El proceso six sigma se caracteriza por 5 etapas
• Definir, consiste en concretar el objetivo del problema y validarlo.
• Medir, consiste en entender el funcionamiento actual del problema.
• Analizar, averiguar las causas reales del problema.
• Mejorar, permite determinar las mejoras procurando minimizar la inversión.
• Controlar, garantizar la continuidad de la mejora y valorarla en términos económicos y de satisfacción del cliente.
¿Por qué adoptar la metodología Lean?
Los equipos de desarrollo de productos y servicios ya no pueden permitirse el lujo de largos plazos de entrega, los competidores están en todas partes, dispuestos a captar a nuestros clientes y hacerse con una parte de cuota de mercado. Lean permite a la empresa optimizar toda la cadena de valor y lanzar productos y servicios que brinden valor a los clientes cuando, donde y como lo deseen. Al aprovechar estas prácticas con una solución de tecnología sólida, la dirección consigue priorizar las acciones correctas a realizar, reducir los esfuerzos desperdiciados y detectar y responder rápidamente al mercado dinámico.
Errores más comunes al implantar Lean Manufacturing
Una de las principales razones por las que falla la aplicación de esta metodología es la incapacidad de hacer un cambio cultural en toda la empresa. La adopción de Lean debe estar impulsada desde la Dirección de las organizaciones y sus mandos directivos deben estar implicados personalmente en todo el proceso, para así garantizar la sostenibilidad y desarrollo del sistema.
Una buena toma de decisiones por parte de la dirección, como bloquear la necesidad de crear más equipos y reconducir dicha necesidad a mejorar la relación que tienen entre sí, es clave para el éxito del cambio cultural. A menudo, tener muchas islas de equipos no aprovecha el verdadero potencial de estar coordinados y alineados hacia un propósito común. Es mucho más enriquecedor equipos donde exista la participación de personas de distintos niveles jerárquicos, diferentes áreas y con distintos conocimientos, para así contar con enfoques conformados por diversas perspectivas.
Por otro lado, es frecuente que la dirección comience la implementación reduciendo stocks o procesos innecesarios, mientras que puede existir una cantidad excesiva de demandas de usuarios que no están siendo valoradas y analizadas previamente. Esto no quiere decir que las decisiones adoptadas en un primer momento no sean importantes o válidas, pero habría que priorizar aquellas de impacto directo con el cliente y que permitan agregar mayor valor a nuestra organización a ojos del usuario final.
Un punto a tener en cuenta es no generar exceso de procedimientos y registros que luego signifiquen un impacto en la calidad del producto. Hay que buscar ideas innovadoras y sencillas de realizar en la práctica.
El método de Lean Manufacturing nunca termina pues lo que se busca es obtener una mejora continua que no permita nuevos estancamientos ni retrabajos. El poder analizar los índices de mejora es de gran ayuda para evitar futuros problemas. Si no se puede medir, no se puede mejorar.
Conclusión
Como conclusión podemos expresar que la implantación de Lean Manufacturing y sus herramientas, trae consigo un reto para la dirección insignificante si lo comparamos con las ventajas que aporta. Aplica una cultura de adaptación al cambio, sobre-posicionamiento ante nuevos competidores, foco y mejora en la atención al cliente, de manera constante y continua. Quienes deciden adoptar esta metodología, cuentan con herramientas para enfrentarse a cualquier tipo de adversidades a tiempo y con el menor impacto posible, mientras que logran que su organización se mueva de manera conjunta para alinearse con los objetivos estratégicos.